Plant Safety and Risk Management
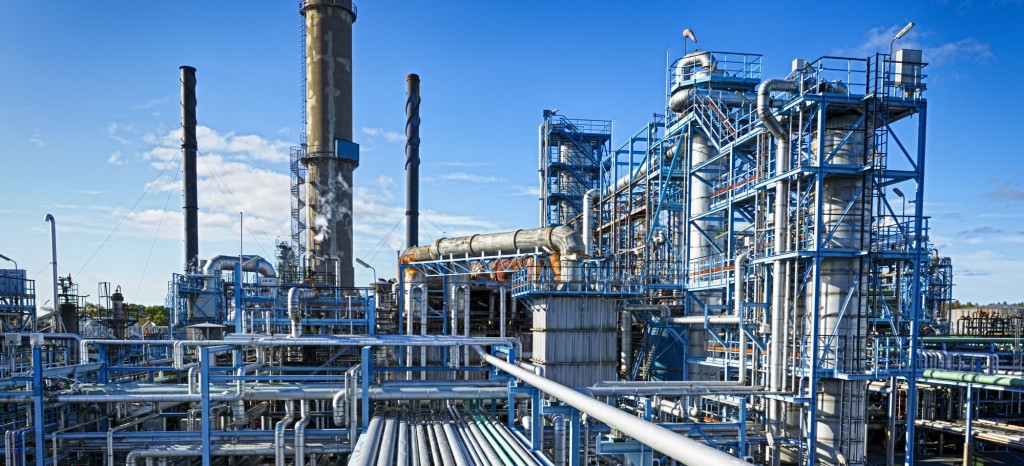
Specialized Risk Management
The operation of plants of all kinds (e. g. chemical and nuclear plants, refineries, power plants, transport and loading facilities) requires a high level of safety in order to avoid threatening the environment or endangering the health of employees and local residents. Specialized risk management tools provide customized solutions to reduce and manage the risks posed by your plant.
With our specialized risk methods and hazard analyses such as HAZOP, HazID and LOPA we systematically identify weak points and increase the availability of your plants at the same time. This also creates the foundation for an installation and operational management of the plants that complies with the legal requirements and regulations.
Benefit from our extensive experience in the area of plant safety and risk management and build trust among authorities, employees, local residents and the public.
Have the safety of your plant inspected. Contact our experts today!
Process Optimization and Risk Assessment of Your Plants
With our plant safety services, you optimize your processes and ensure a smooth operation of your plant by implementing a comprehensive safety management. By complying with the regulatory requirements, you not only fulfill your operator's responsibility, but also reduce the risk of events of damage and thus save additional costs that would arise in the event of a production stop or downtimes.
Our Services Related to Your Plant Safety and Your Risk Management
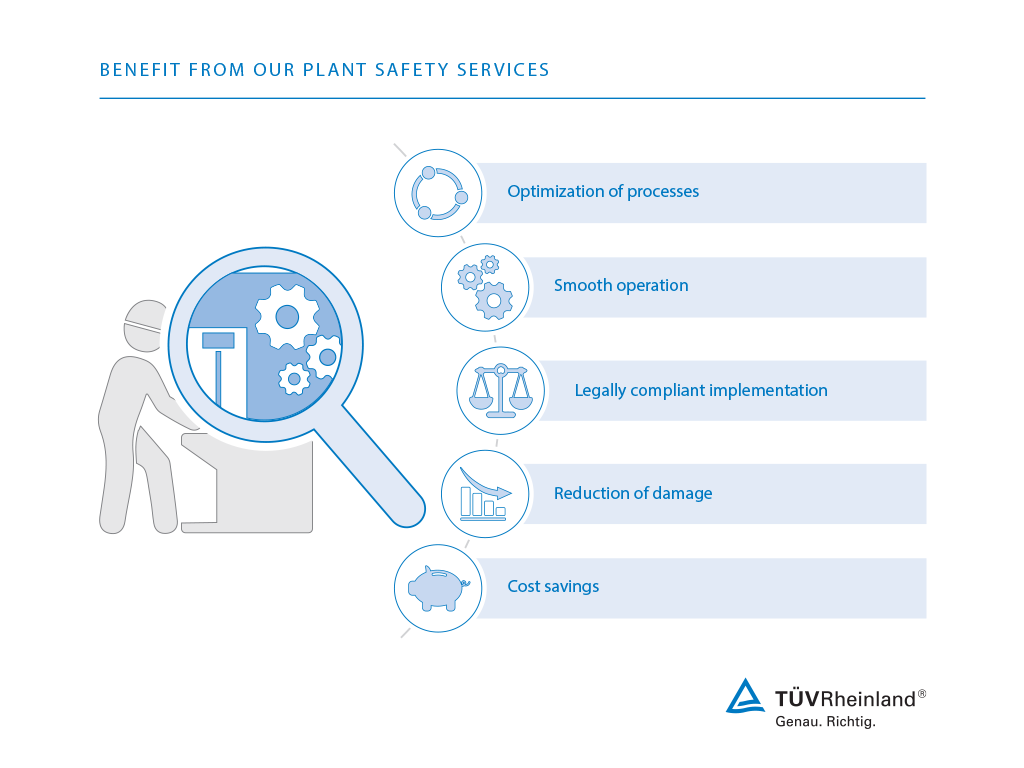
Our range of services for the safe operation of plants of any kind (e. g. chemical and nuclear plants, refineries, power plants, transport and loading facilities) includes services such as:
- Approval procedures and safety analyses
Safety reports and safety concepts to prevent incidents, safety-related inspections, risk analyses based on recognized methods such as HAZOP, HazID or LOPA, damage investigations and safety-related plant inspections - Risk Management
Safety management system based on the Hazardous Incident Regulation, Disaster Management (DISMA) , support with SIL classification, project management and dealing with authorities - Audits and Trainings
Safety management systems and procedures, operating organization, HSE procedures, etc.
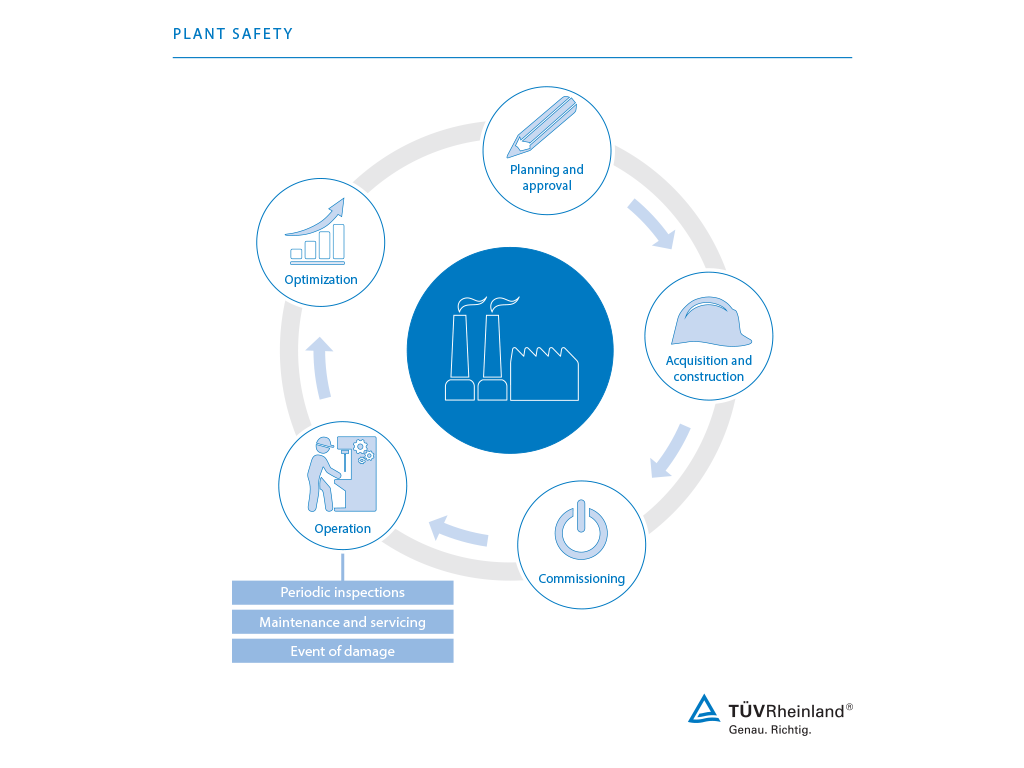
We assist you throughout the entire life cycle of your plant. Our range of services provides support in the following areas:
- Concepts for the prevention of incidents
- Safety management systems
- Safety reports
- Safety-related inspections
- Dispersion calculations
- Risk analyses based on recognized methods such as HAZOP, HazID or LOPA
- SIL classification
- Explosion protection documents
- Emergency plans
- Damage investigations
- Disaster prevention
Benefit from our Long-Time Experience in Incident Prevention
Our experts have an extensive experience in the area of plant safety. We offer you a global network of experts and comprehensive services as a one-stop solution. Our experts are active in a variety of committees and bodies, which enables us to provide you with competent support in all safety-related issues from planning your plant to damage control.
Learn more about our plant safety services. Make an appointment with our experts!