amfori QMI audits (Quality Management Initiative)
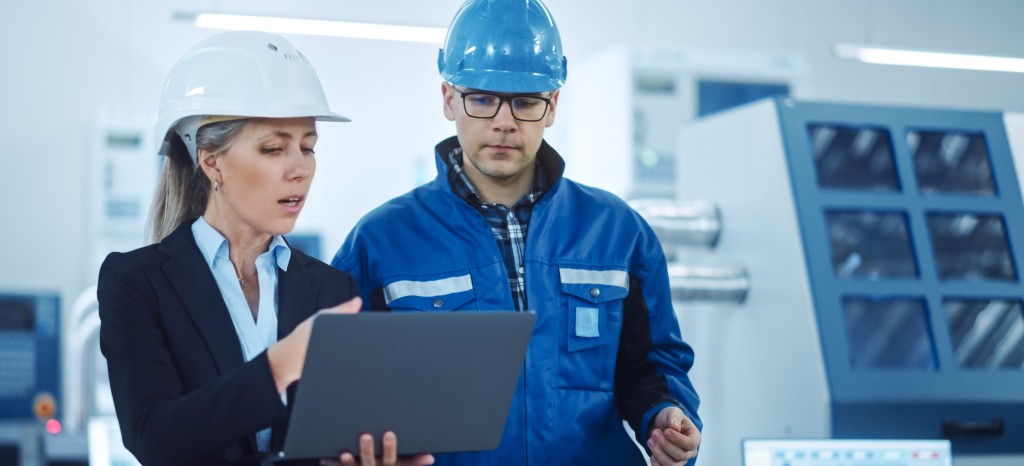
Enhancing quality and sustainability with amfori QMI audits
amfori QMI is an initiative designed to offer professional guidance and assessment tools for manufacturing and quality management. By setting a universal standard for non-food industries, amfori QMI seeks to avoid audit fatigue, reduce audit costs, and jointly monitor sustainability risks of quality management in global supply chains. Contact our experts to learn more.
Our approach to factory (supplier) monitoring
Quality management capability has been the pre-requisite to start sustainable sourcing and build a responsible supply chain for many global buyers, brands, and retailers. Most non-food sourcing (retail) organizations have developed their own auditing program, creating their own audit checklist(s) integrated in their supplier’s qualification program. As a result, there is a duplication of efforts, waste of resources, inconsistent scoring, and assessments, which all creates unnecessary confusion.
In response to the needs of amfori members for a holistic strategy to manage sustainable supply chains, amfori launched a pilot program in China from August 2020 to Q2 2021. This initiative was supported by amfori members and the German Chamber of Commerce in HK. As a result, amfori QMI was founded in Q1 2022 and provides a set of standardized quick scan tools that enable companies to drive quality management capability improvements in their supply chain and to trade with purpose. amfori QMI covers a scope of 4 quality management capability aspects including:
- Infrastructure, System and Environment
- Product Design
- Incoming Materials Quality Control
- Production Control
Discover the key benefits of amfori QMI
Benefits for amfori members:
- Reduce the overall resources towards producers/suppliers’ qualification/assessment
- Avoid duplication of factory audits for the same purposes & requirements
- An integrated approach of managing sustainable buyer-supplier relationship in a holistic manner – social, environmental, and technical quality integrated in one-stop platform
- Use this common standard to benchmark and screen new sustainable producers
- Strategic and multi-dimensional monitoring of multiple producers’ quality management capability to further engage producers in a long-term sustainability performance improvement via amfori
Benefits for producers supplying amfori members:
- Avoid audit fatigue and reduce audit costs
- Effective management of multiple audits with one common auditing tool via amfori links to visible return-on-investment (ROI)
- Build and maintain customer retention, trust, and satisfaction
Self-Requested Monitorings – How It Works
Starting from 2 July 2025, amfori business partners can directly request monitorings for their own sites under the following programs: amfori BEPI, amfori BSCI, and amfori QMI. This new functionality on the amfori Sustainability Platform empowers business partners to proactively ensure continuous compliance.
Key Requirements for Self-Requested Monitorings:
- The business partner must be linked to at least one amfori member.
- No linked member may have already initiated the monitoring.
- Linked members must not cancel the request within 5 calendar days after submission.
- The monitoring must be paid for directly by the business partner—third-party payments are not permitted.
TÜV Rheinland can provide support with the implementation of self-requested monitorings. This includes guidance throughout the monitoring process as well as clarification on how the self-request functionality works within the amfori Sustainability Platform. Need help with self-requested monitorings?
Explore the value of choosing amfori QMI
- amfori offers a set of quick scan auditing tools that enable their members to identify the best practices as well as insufficient areas for improvements of producers in quality management of their production sites.
- The amfori QMI platform provides a single point for the amfori QMI audit results, while the amfori sustainability intelligence dashboard helps users clearly visualise complex supply chains. These tools help amfori members identify areas for improvement, compare data across the global supply chain and transform information into concrete insights and actions. They can then track and measure progress to support targeted improvements. It is a good supplementary tool to enable members’ holistic and integrated approach in pursuing responsible sourcing and sustainable supply chains.
TÜV Rheinland: Your trusted partner for amfori QMI Audits
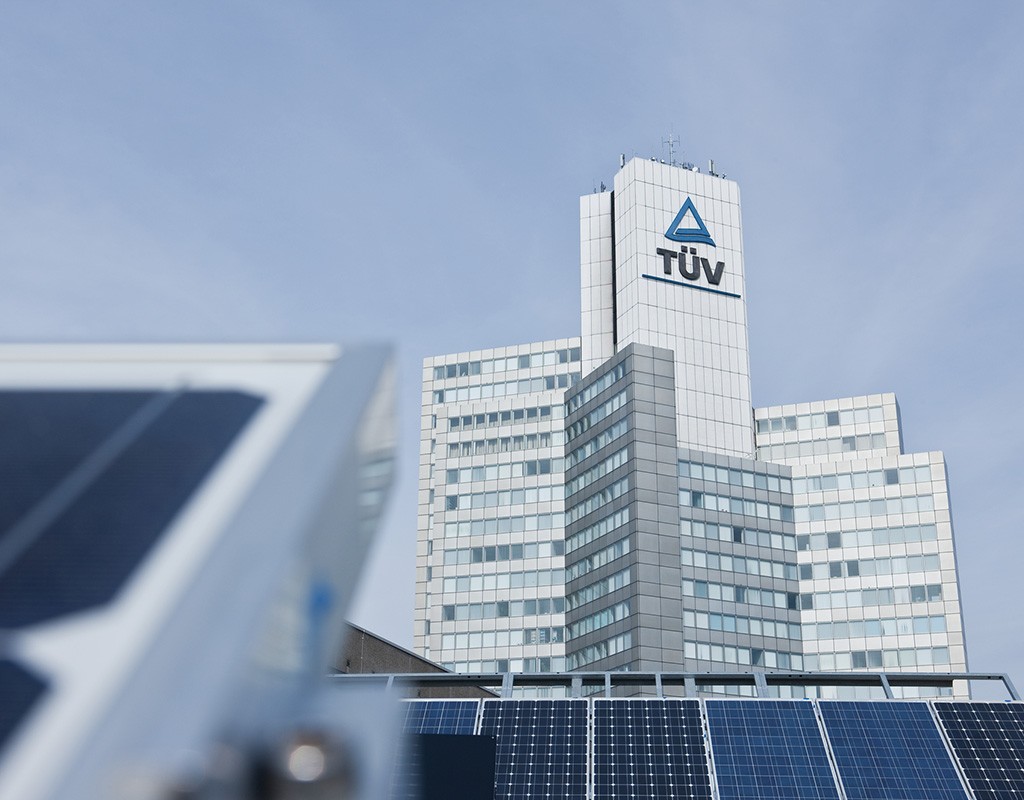
TÜV Rheinland is a global leader in independent inspection services. Established 1872 in Germany, TÜV Rheinland inspects technical equipment, products and services, oversees projects and helps to shape processes for companies and audits management systems and evaluates suppliers.
For over 20 years, TÜV Rheinland has monitored working conditions in the global supply chain by conducting audits based on various customer-specific codes and international standards such as BSCI, SA8000, RBA, SMETA, ISO 9001, ISO 14001 and ISO 45001.
Important Links
Downloads
amfori QMI – Easy Guide for Producers | 330 KB | Download |
Contact our experts in your region for a personalized quote.
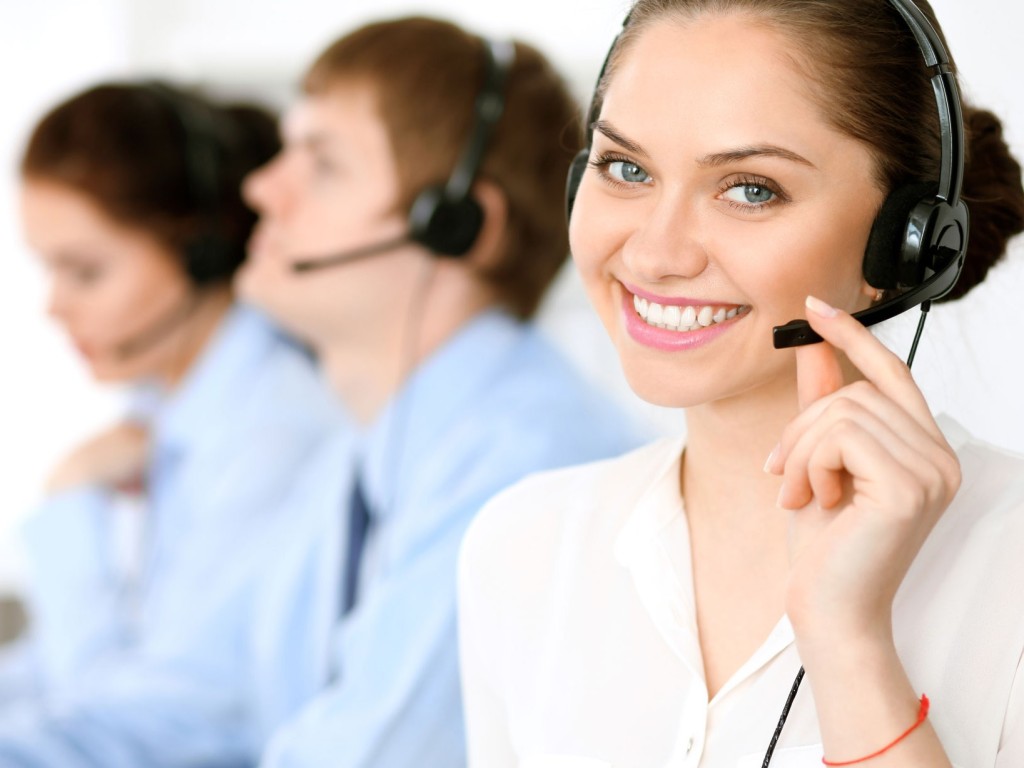