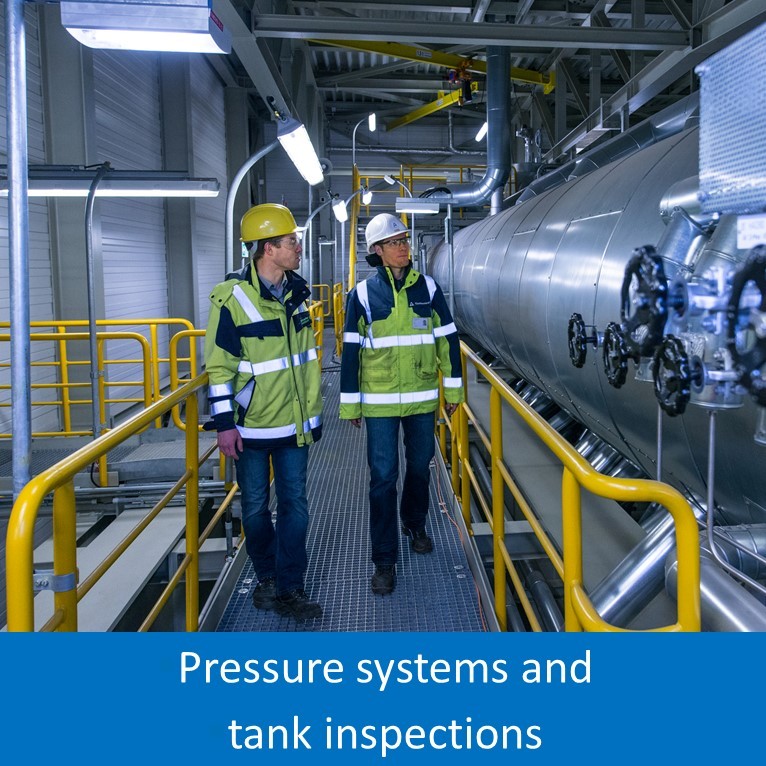
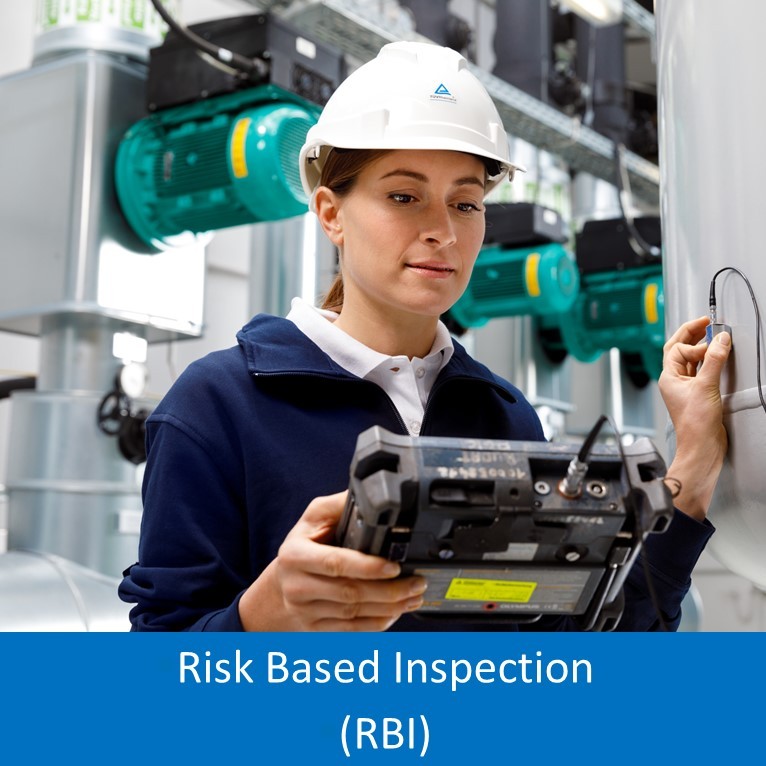
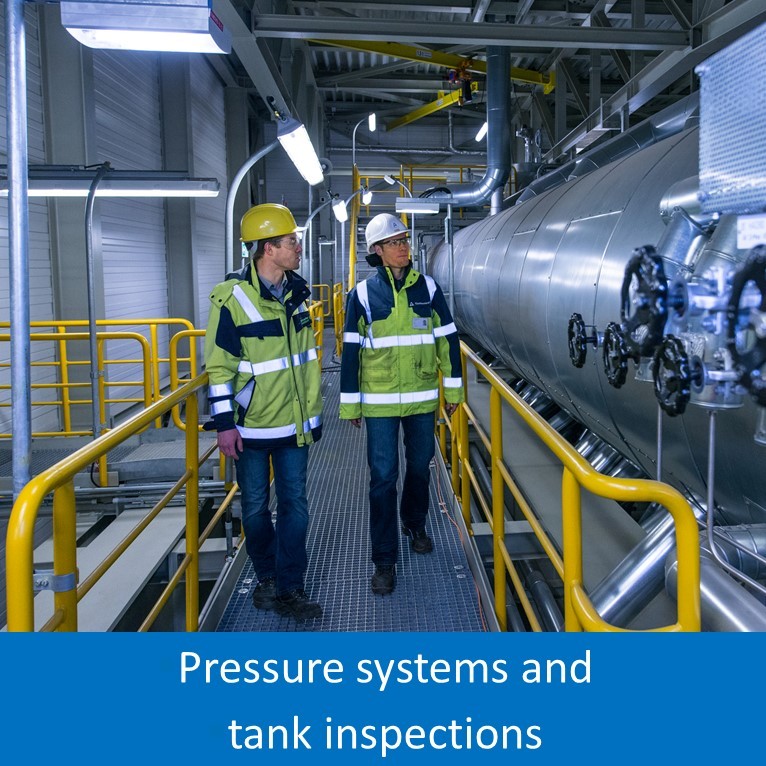
Leading provider of 3rd party pressure systems inspections in the UK and the North Sea.
Accredited by the United Kingdom Accreditation Service (UKAS), TÜV Rheinland supplies a full inspection service - inspection scheduling and planning, inspection and reporting, reviewing and updating schemes of examination.
The TÜV Rheinland approach is to develop risk based schemes of examination that focus the inspection effort into the areas of highest risk. This approach leads to more effective and cost efficient inspections and optimises the amount of NDT work required.
TÜV Rheinland's inspection team works closely with its design team and through specialist design services advises on defects found during inspection and their rectification.
Our inspection services are applied to pressure systems covered by the Pressure Systems Safety Regulations (PSSR) and to other related equipment, such as pipework and tanks.
Management of plant integrity.
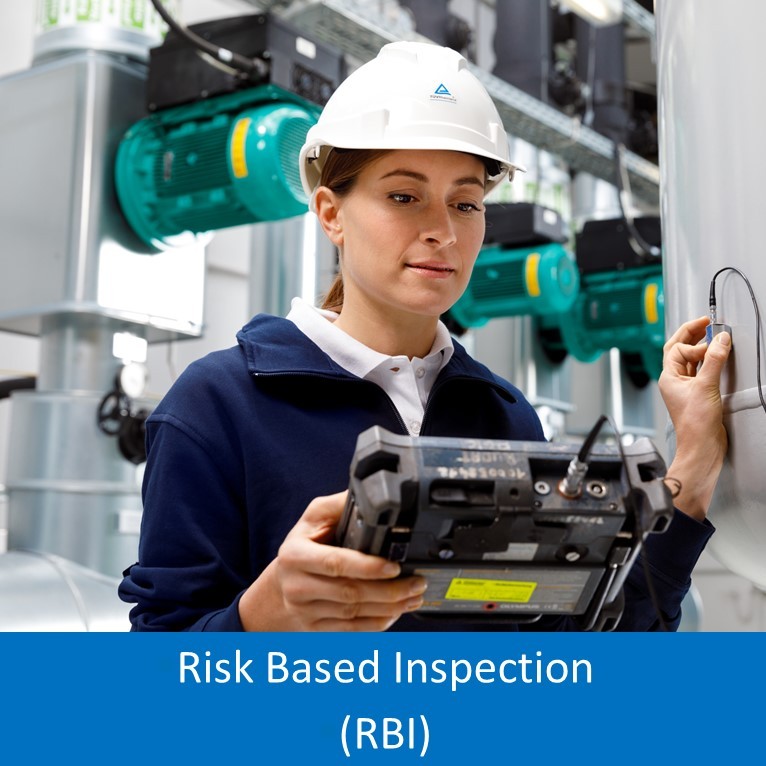
TÜV Rheinland provides a range of Risk Based Inspection (RBI) consulting services:
- RBI studies - using our proprietary methodology and tools
- Focussed schemes of examination service - updating inspection schemes to reflect the outcomes for RBI studies
- Screening studies - a rapid assessment of equipment to prioritise items for full RBI studies
Our approach to RBI uses qualitative and semi-quantitative methods utilising real operating experience to optimise inspection schemes and intervals. RBI can be carried out on a variety of types of equipment (e.g. pressure systems, rotating equipment, structures, etc.). Our RBI approach follows TÜV Rheinland’s RBI+© methodology and uses the RBI+© pRIME tool. To see how RBI+© pRIME software can benefit your business try our free demo at: www.prime-toolkit.com
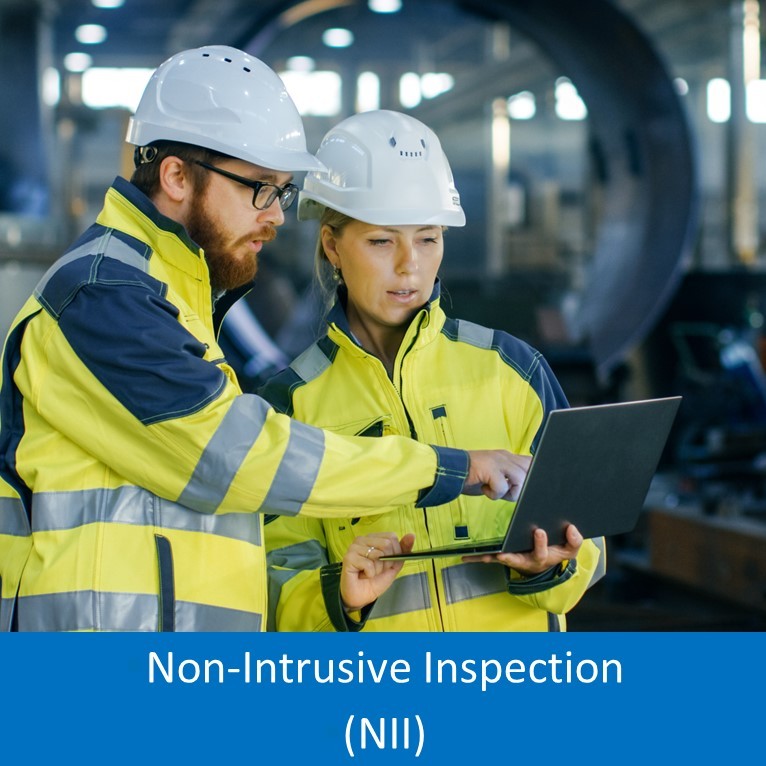
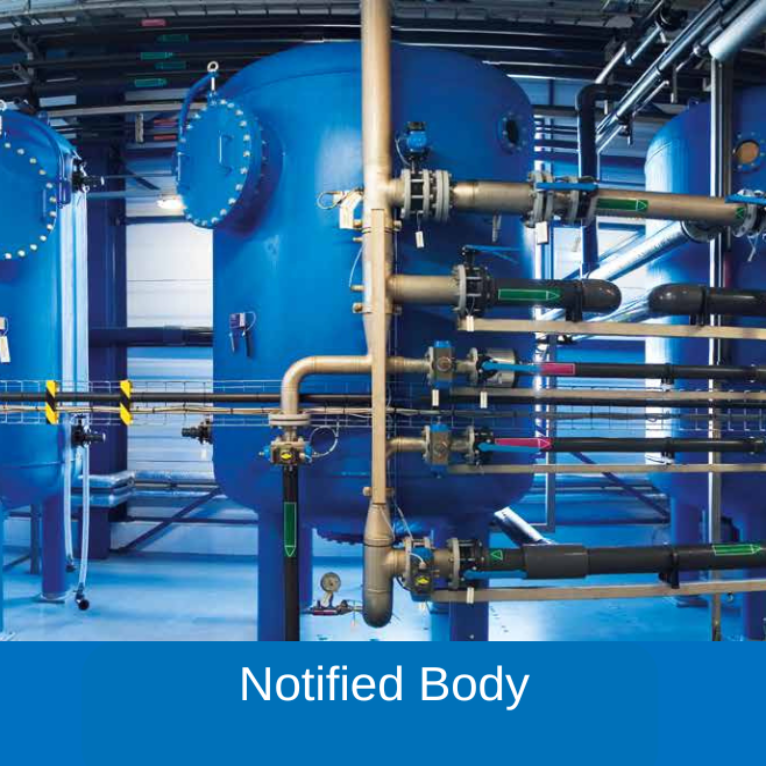
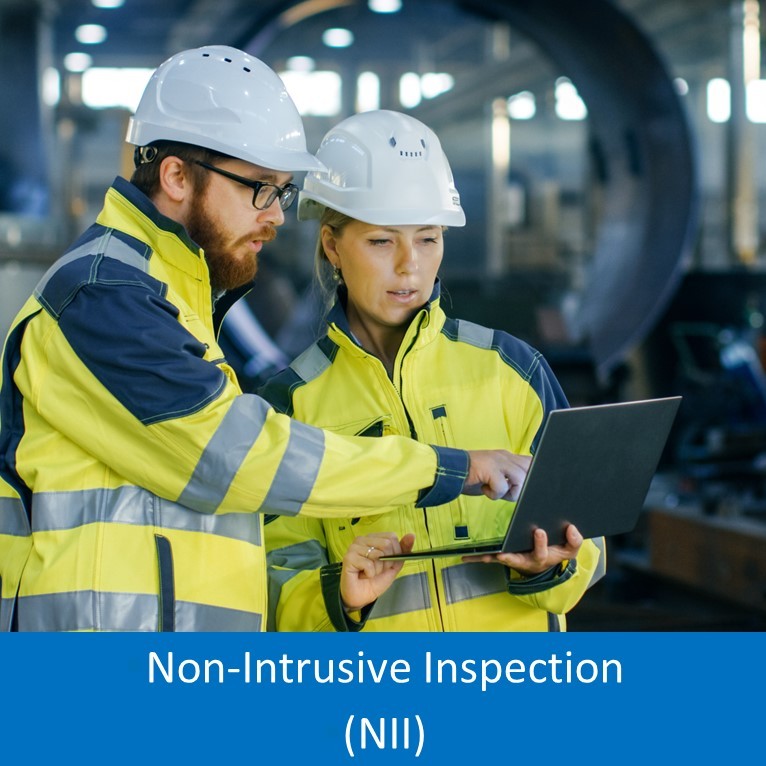
Non-Intrusive Inspection (NII) and Specialist NDT
Non-intrusive inspection (NII) is a process in which planning and evaluation of an external inspection allows replacement or deferment of internal inspection. In certain circumstances, some NII inspections can be also performed on-stream at high temperatures, when the plant equipment is still operating. NII provides operators with key benefits including reduced number of confined space entries and increased production uptime and lower maintenance costs. Consequently, NII is considered as an attractive option where appropriate and safe to do so. Especially in the petrochemical, process, gas and conventional power industry, on-stream inspections can significantly reduce the duration of planned shutdowns. Such pre-turnaround inspections enable Inspection and Maintenance Managers to accurately assess the inspection and maintenance scope, and to prepare in advance for the required repairs and maintenance.
Non-Intrusive Inspection can be specified by careful assessment to address all relevant damage mechanisms and replace with suitable NDT method(s) of equivalent or better results than Internal Visual Inspection. TÜV Rheinland personnel are familiar and experienced with this methodology and are able to carry out NII assessments to the recognised recommended practice of HOIS-RP-103. The NII assessment report will determine the required NDT and/or monitoring techniques at specified locations and the level of coverage to satisfy the recommended practice.
NII approach is especially effective for:
• detection, location and sizing of in-service weld defects,
• corrosion mapping of the vessel and / or piping surfaces,
• active corrosion and leak detection,
• inspection of Corrosion Under Insulation (CUI) and Corrosion Under Pipe Support (CUPS)
• early detection and monitoring of High Temperature Hydrogen Attack (HTHA)
• Automated Corrosion Rate Monitoring through wireless sensors
We help you to reduce the scope of scheduled turnarounds and to minimize the HSE risks, especially during the Life Time Extension of your critical equipment. We offer a broad portfolio of specialist Advanced NDT methods such as TOFD, PAUT, AET, LRUT, PEC, High Temperature NDT, corrosion mapping, and specialist / bespoke NDT applications to support and gain the benefits of NII and to reach your individual goals.
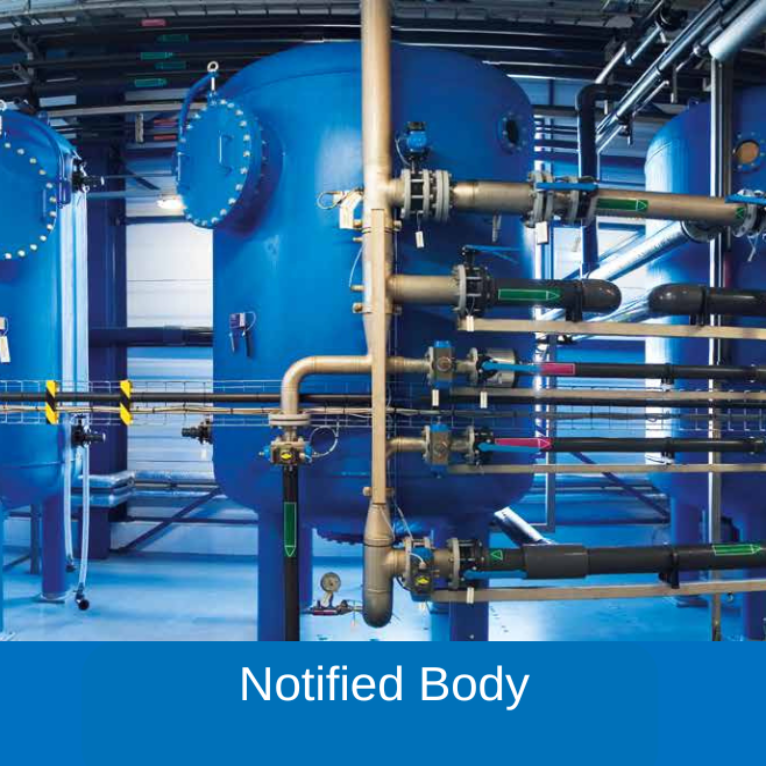
At TÜV Rheinland, we understand the critical importance of compliance with the Pressure Equipment Directive (PED) 2014/68/EU for manufacturers of pressure equipment. As a leading Notified Body, we offer a full and comprehensive range of services to ensure your products meet the stringent safety and performance standards set by the PED. Our expert team conducts thorough product testing, conformity assessments, and certification processes, alongside detailed audits of your quality management systems. Among the services we provide are:
• Design examination of each item of pressure equipment
• Design examination of assemblies, including examination of safety devices such as the design and suitability of measurement and control protective equipment, circuit diagrams, suitability of electronic components, PCE-devices, and safety valves
• Qualification of welding operators and joining processes
• Qualification of NDT personnel
• Particular material appraisals, such as when using ASME materials under the provisions of the PED
• Single approval of pressure equipment or assemblies under Modules F and G
• Issuance of type approvals under Module B (design and production type)
• Auditing of QA systems under modules D/D1, E/E1, and H/H1
• Auditing of QA systems of material manufacturers in accordance with Section 4.3
• Type 3.2 inspection certificates according to EN10204:2004
By leveraging our extensive experience and technical expertise, TÜV Rheinland ensures that your pressure equipment meets all regulatory requirements and performs reliably in its intended applications. Partnering with TÜV Rheinland for Notified Body services not only helps you demonstrate PED compliance, but also enables you to confidently place your products on the European market carrying CE or UKCA certification marks.
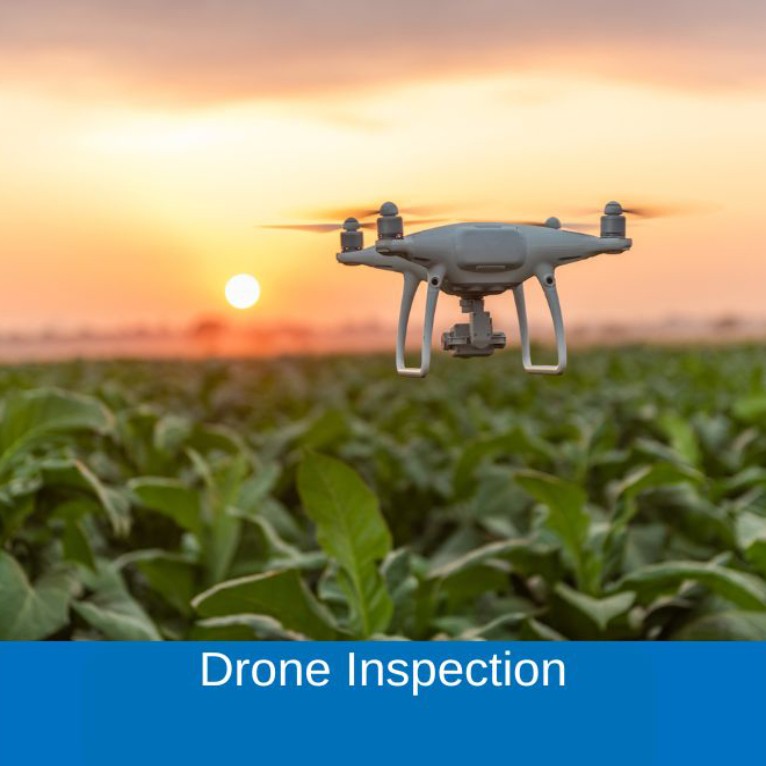
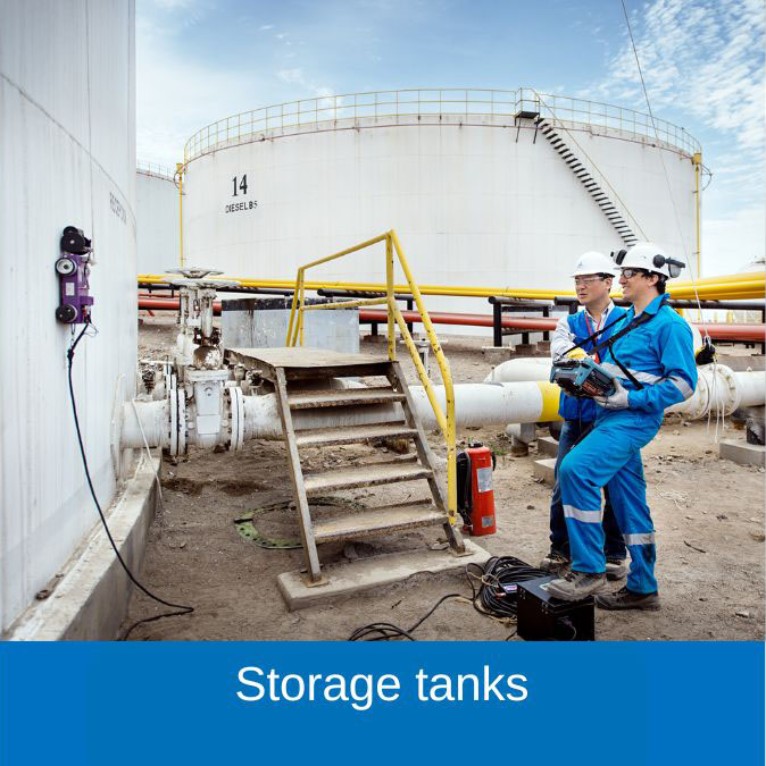
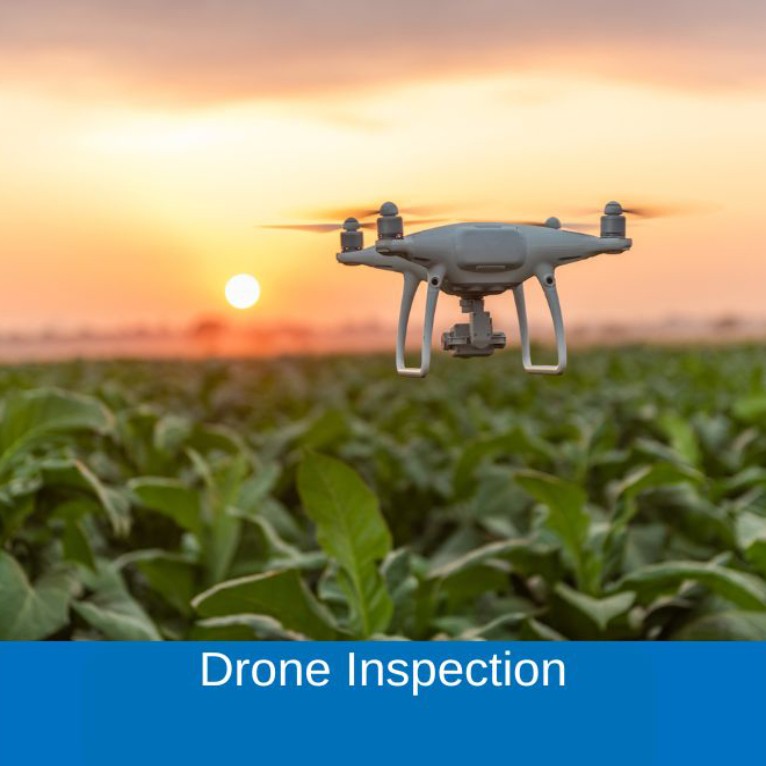
TÜV Rheinland inspectors leverage the latest advancements in drone technology to provide comprehensive drone inspection services for both external and internal assessments of your equipment. Our drone inspections offer a safe, efficient, and cost-effective solution for evaluating the condition of assets, even in the most challenging environments.
External Drone Inspection: Our external drone inspection services are ideal for assessing the condition of hard-to-reach areas such as rooftops, flare stacks, chimneys, and large storage tanks. Equipped with high-resolution cameras and advanced sensors, our drones capture detailed images and videos, allowing for precise analysis of structural integrity, corrosion, and other potential issues. This method minimises the need for scaffolding, cranes, and other costly and time-consuming access solutions, while also significantly reducing the risk to personnel.
Internal Drone Inspection: For the inspection of internal spaces, such as pressure vessels, storage tanks, and other confined spaces, our drones are equipped with specialised lighting and camera systems to navigate and document these environments. Internal drone inspections eliminate the need for personnel to enter hazardous or confined areas, enhancing safety and reducing the preparation time associated with traditional entry methods. These inspections can quickly identify cracks, corrosion, and other defects that could compromise the integrity of the equipment.
By employing drone inspection technology, TÜV ensures that your equipment is thoroughly evaluated with minimal disruption to operations. Our expert team analyses the collected data to provide you with detailed reports and actionable insights, helping you maintain the highest standards of safety, compliance, and operational efficiency. With drone inspections, you can achieve significant cost savings, improve safety, and ensure the reliability of your assets.
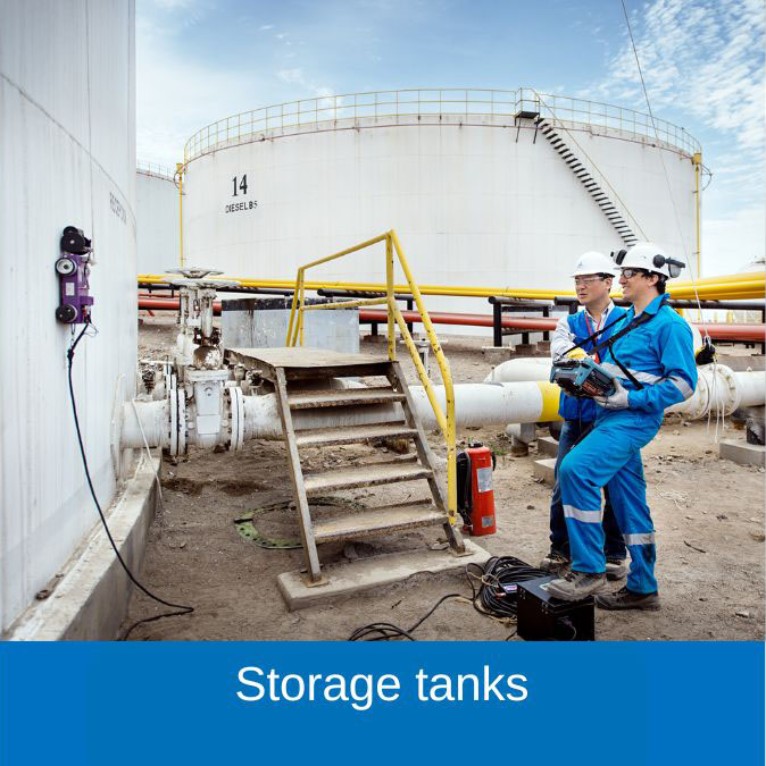
At TÜV Rheinland Industrial Services, we support clients throughout the entire lifecycle of their storage tanks.
Our offerings include inspection and NDT, integrity lifecycle management, process safety, late-life services and decommissioning.
Using our dedicated pRIME inspection and RBI management system, we provide detailed and actionable reporting that help operators to effectively manage safety and mechanical integrity of their assets. Our holistic approach ensures that from initial installation to decommissioning, your storage tanks are managed with the highest standards of safety and integrity, meeting all performance, safety and quality requirements.