contact - knowledge magazine awarded
AWAREness
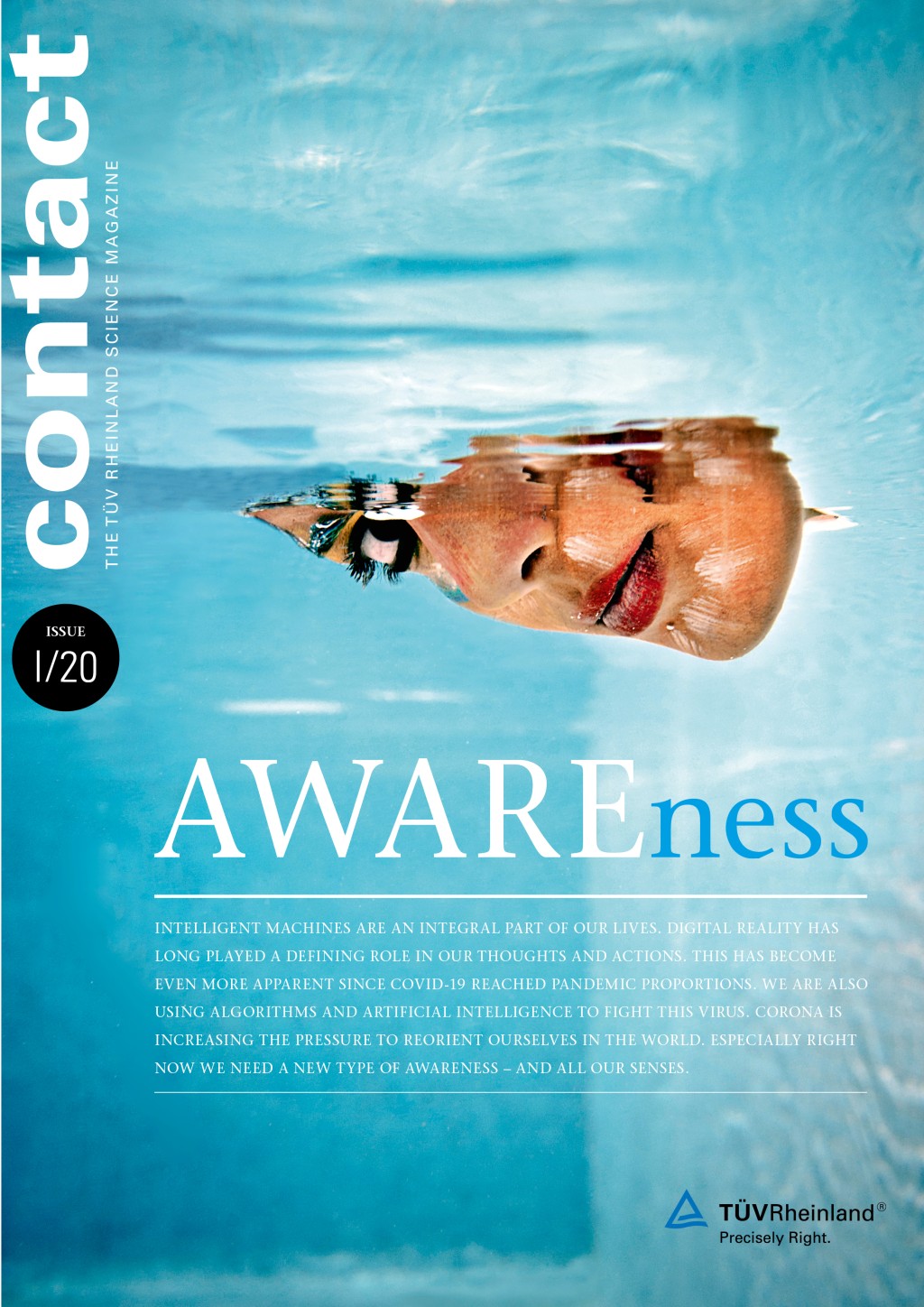
Intelligent machines are an integral part of our lives. Digital reality has long played a defining role in our thoughts and actions. This has become even more apparent since covid-19 reached pandemic proportions. We are also using algorithms and artificial intelligence to fight this virus. Corona is increasing the pressure to reorient ourselves in the world. Especially right now we need a new type of awareness – and all our senses.
Please have a look at the current issue of our knowledge magazine contact - available as flippable PDF-file.
Click
here!
Click
here
to download!
AWAREness
Dr. Michael Fübi: “Important and really important”
The Corona crisis has completely changed our lives. Finding our way in this new world is more than ever a big challenge. In addition to all the technology, it is now necessary to trust our own senses.
Remain sensitive
Digitalization takes over a lot for us. We reproduce our senses with technology and artificially augment
them. But dealing with Alexa, Siri and modern image recognition software significantly changes our awareness and perception. We are well-advised to remain sensitive despite all the technology. Because the digital helpers can be outsmarted and manipulated.
Precise tracking
Whether steps, calories or blood values: fitness trackers worn on the body measure and monitor the person’s daily behavior and physical performance. What role do these devices play for human self-perception and the health system?
Dr. Christian Schemer, Professor of Communication at the Institute of Communication in Mainz, Germany, knows how language determines our perception of reality. Dr. Caroline Beier, Chairwoman of the German Synesthesia Society, explains how synesthetes perceive the world. Aroma and smell researcher Professor Dr. Andrea Büttner uses the sense of smell to “sniff out” harmful substances in products.
Also in this issue:
All-powerful high-speed Internet: In order to guarantee widespread, stable Internet coverage, a dense satellite network is required. Topography and local infrastructure no longer play a role in this.
Critical forest morphosis: The forest is both an economic factor and the basis of life. Its influence on the environment, the climate and on mankind is undisputed. But the state of the world’s forests is not good. How can sustainable forest management work?
New World: Matthias Horx is a trend forecaster and future researcher. In our interview he talks about his concept of Re-gnosis and why this method can give hope especially in the Corona crisis.
Download or print contact magazine
Current issues of the knowledge magazine as pdf:
Knowledge magazine contact 2.19
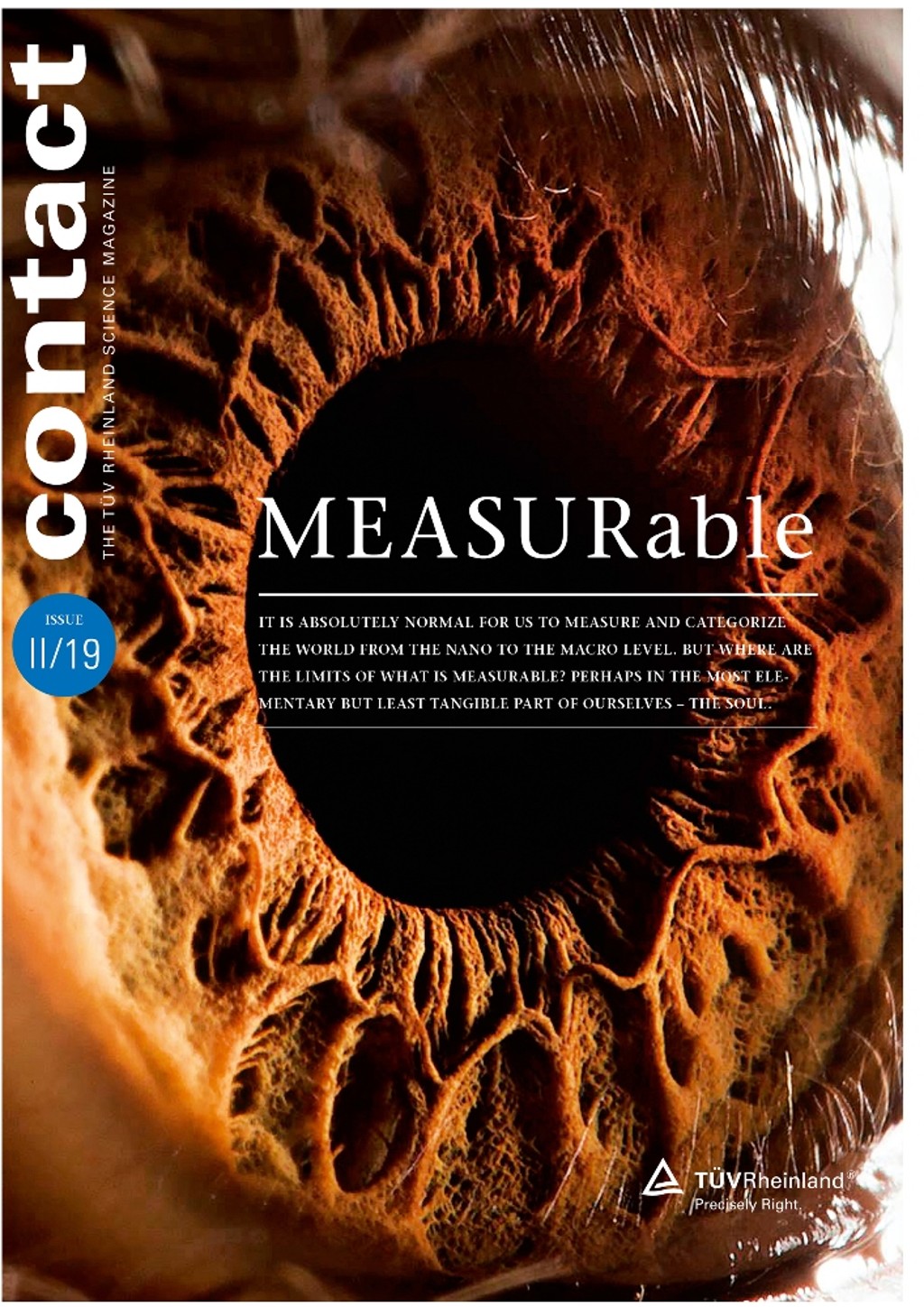
MEASURable
It is absolutely normal for us to measure and categorize the world from the nano to the macro level. But where are the limits of what is measurable? Perhaps in the most elementary but least tangible part of ourselves – the soul.
Click
here
to download!
Contact
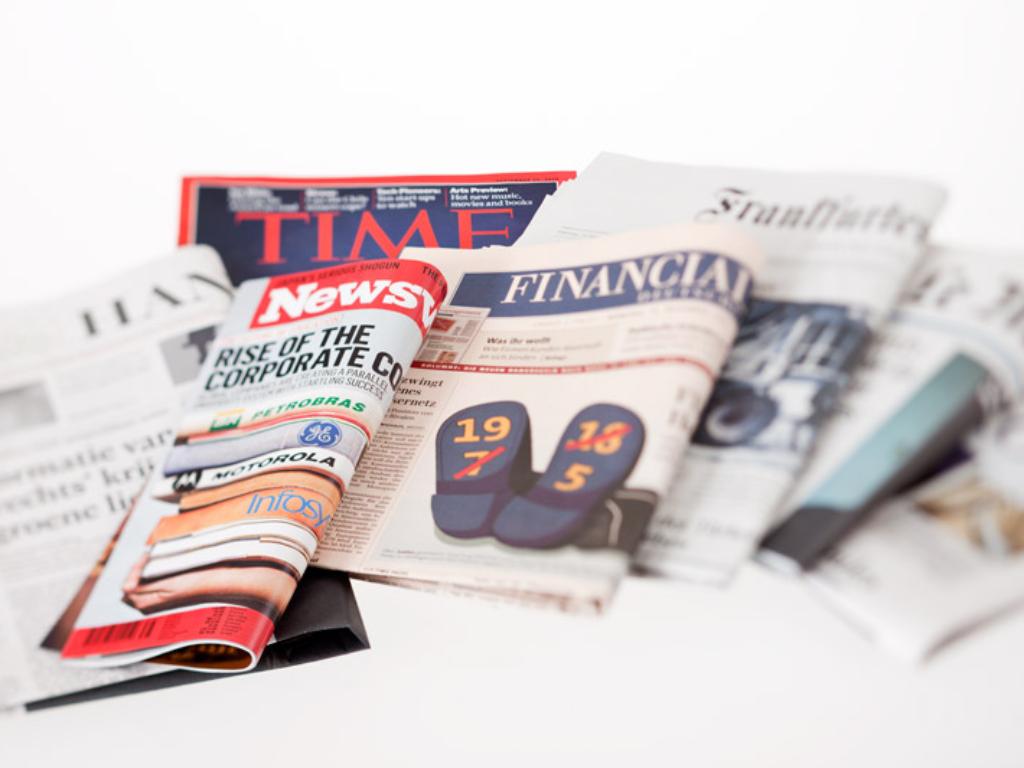